In this jointing technique the two pipe ends are clamped in a hydraulic moving carriage which provides a basis for a number of secondary operations, as follows:
- The pipe ends are trimmed so that they are clean, and so that when brought together or aligned there should be no visible gap or step between them.
- The pipe ends are then heated simultaneously against a double-sided flat heater plate for a specific time and at a specific pressure, depending on pipe diameter. This stage generally includes a ‘soak’ phase with heat continuing to be applied but with virtually no pressure, to ensure the pipe absorbs enough heat to provide a secure joint.
- Following the heating cycle, the ends are brought together, again under pressure, to form a complete joint. After a specific cooling time, the Butt-Fusion machine is removed, for assembly onto the next joint. (In hotter climates, it is recommended that the cooling times are doubled).
- The cooled joint should be inspected for bead size and cleanliness. De-beading of the joint provides an additional means of assessing joint quality.
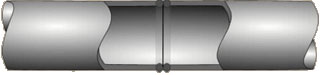
Butt-Fusion jointing provides an ideal method for size-to-size replacement work, giving maximum possible capacity in new pipes within existing lines.
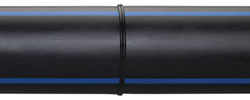